Dans les secteurs de l’industrie agro-alimentaire et du commerce « de bouche », la production de froid représente un poste de dépense important pouvant aller jusqu’à 50% et même 70% selon les cas, de la facture d’électricité.
La production du froid industriel représente près de 9% de la consommation nationale d’électricité. Le secteur agroalimentaire consomme à lui seul 57% de l’électricité consacrée au froid. Cela est lié aux besoins énergétiques importants des procédés de fabrication et aux exigences en matière de sécurité sanitaire (transformation de produits humides, séchage, combustion, chaîne du froid, …).
L’énergie représente donc un défi environnemental et un enjeu de compétitivité important pour le secteur ; c’est en moyenne le second poste de coût de production derrière les matières premières.
Au vu de l’importance de ce poste de dépenses, les industriels ont bien sûr pris les mesures nécessaires pour éviter les gaspillages. Les premières mesures concernent évidemment l’éducation et la sensibilisation des personnels qui travaillent dans ces installations. Une porte de frigo mal fermée, une température trop froide : cela conduit à des dérives et surcoût de consommation.
Il est une autre source de gaspillage qui est moins évidente et moins connue par un grand nombre de responsable du froid, ce sont les équipements eux-mêmes. Des mauvais réglages, des dysfonctionnements non détectés, des entretiens non effectués vont immédiatement alourdir la facture.
ENERGY SOLUTION entreprise de services énergétiques spécialisée dans le froid et fluides industriels a pu le constater. Avec 30 ans d’expérience accumulée dans la conception et la mise en route de système industriel a ainsi identifié de nombreuses sources de gaspillage et peut ainsi maintenant proposer des solutions correctrices. Les économies d’énergie réalisées suite à la mise en place des solutions a conduit parfois jusqu’à 50% d’économie.
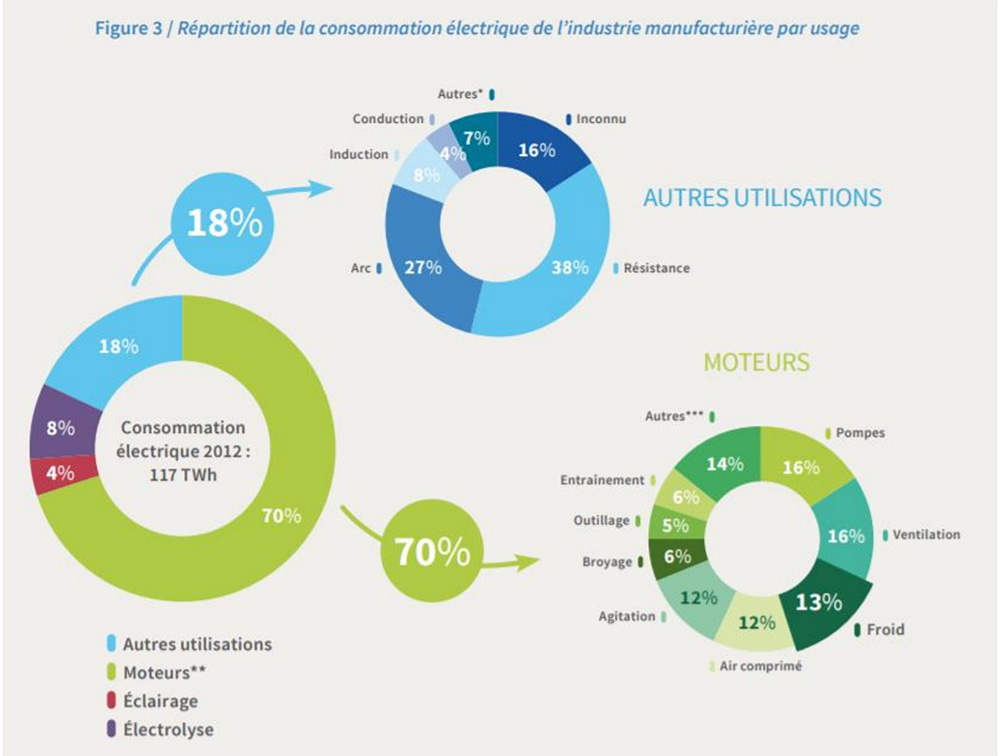
Comment cela est-ce possible ?
Le froid est d’une manière ou d’une autre, produit par des moteurs. Le graphe ci-dessous est assez clair. 70% de l’électricité est consommée par des moteurs, et les moteurs dédiés à la production du froid représente 13% de l’ensemble de cette consommation, soit 9 % comme indiqué en
introduction.
Ainsi en associant les paramètres moteurs aux autres paramètres du système, température, hygrométrie, heures d’ouverture, etc. Il est possible avec les algorithmes de l’application TIME4.0 développée par ENERGY SOLUTION de détecter les dérives, et les gisements d’économie potentiels d’énergie.
Cela passe par l’exploitation d’un plan de comptage existant et/ou la mise en place d’un plan de comptage pertinent adapté à chaque site. L’ensemble des compteurs électrique, eau, gaz, etc. sont connectés au système, un ensemble de capteurs et sondes diverses aussi connectés sont aussi ajoutés en fonction de chaque problématique.
Chaque donnée d’information est ainsi récoltée en temps réel et est transmise à travers un réseau de retour vers le serveur de l’application TIME 4.0. Basé sur les principes de la norme IPMVP (International protocol of measurement and verification protocol), les algorithmes d’experts traitent les informations pour à la fois une gestion opérationnelle optimum du site industriel, et une surveillance permanente des dérives et problèmes ponctuels.
Avec ce système de surveillance mis en place et grâce au savoir-faire des experts Energy Solution, il devient facile d’identifier les points de dysfonctionnement, les possibilités d’amélioration des performances. Il sera alors possible sans investissements ou en passant par l’étude et l’installation d’équipements plus performants de réduire de manière très significative la facture énergétique.
Sources :
Comme dans l’ensemble de l’UE, l’utilisation d’énergie est la principale source d’émission de GES en France (71%) (1). L’industrie alimentaire est le 3ème secteur industriel le plus consommateur d’énergie après l’industrie chimique et la métallurgie (2). Cela est lié aux besoins énergétiques importants des procédés de fabrication et aux exigences en matière de sécurité sanitaire (transformation de produits humides, séchage, combustion, chaîne du froid, …). L’énergie représente donc un défi environnemental et un enjeu de compétitivité important pour le secteur ; c’est en moyenne le second poste de coût de production derrière les matières premières. De nombreuses actions ont été mises en œuvre par les entreprises agroalimentaires afin d’améliorer la gestion des énergies : LE COÛT DU FROID
http://www.frigoristes.fr/article.php?sid=265#.XUPe4-gzZnI
Dans les secteurs de l’industrie agro-alimentaire et du commerce « de bouche », la production de froid représente un poste de dépense important pouvant aller jusqu’à 50% de la facture d’électricité.
Le froid industriel représente 4% de la consommation d’électricité française et près de 7% de la consommation nationale d’électricité. Le secteur agroalimentaire consomme à lui seul 57% de l’électricité consacrée au froid.